What to Expect from Professional Industrial Cleaning Services
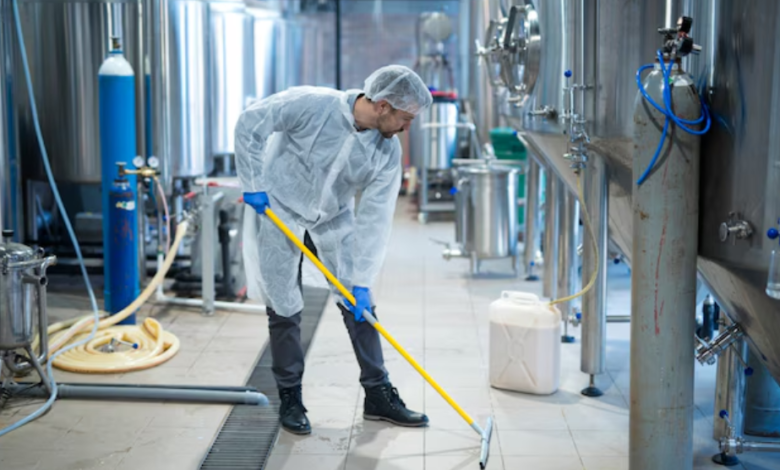
Walk into a spotless industrial unit, and it might feel reassuring. But it’s not really about what’s on the surface. The real purpose of industrial cleaning is deeper—preventing injuries, avoiding damage, and keeping everything legally compliant. Without regular cleaning, even a well-run facility can fall apart fast.
Understanding Industrial Cleaning Services
So, industrial cleaning services—what do they actually include? This isn’t your everyday dust-and-mop routine. It’s more specialised. These services tackle the places that most people ignore. Or don’t even realise they need attention.
Factories, warehouses, and workshops tend to collect things—grease, debris, fine dust, chemical residues. These can’t be handled casually, and in many cases, they shouldn’t be delayed.
Hidden Trouble Spots That Can’t Be Missed
Some of the worst hygiene issues aren’t where people walk or work directly. They build up in forgotten corners, like:
- Overhead beams and racking that trap dust
- Ventilation systems no one’s checked in a year
- Machinery bases where oil and dirt gather
- Storage zones with sticky spills or residue that’s just… there
It adds up. Slowly. But it matters. Neglect one of these long enough, and eventually someone notices—maybe an inspector, maybe a worker getting sick, or maybe when a piece of equipment fails unexpectedly.
Not Every Site Needs the Same Thing
This is where many businesses get it wrong. There’s a tendency to assume cleaning is standardised. But what works in a cold storage facility wouldn’t suit a busy packaging plant. Different spaces call for various tools and methods.
It might include:
- Low-moisture floor scrubbing in areas with electrical gear
- Solvent degreasing where machine oil builds up
- High-powered vacuums fitted with HEPA filters for airborne dust
- Dry ice blasting in sensitive or food-related environments
- Steam cleaning in places where chemicals can’t be used safely
The trick is knowing what suits the site. That only comes with experience—and asking the right questions.
What a Proper Team Brings to the Table
Show up with a mop and a van, and it’s just not going to cut it. Good cleaning teams prepare. They ask questions, check layouts, and inspect surfaces.
Generally, a solid provider will:
- Inspect the site before doing anything
- Point out problem areas, even ones you hadn’t noticed
- Use protective gear that matches the risks
- Work from a schedule that fits your operations, not the other way around
The more effort they put into planning, the less disruption they’ll have later. It’s a detail that makes a big difference.
See also: Why Every Homeowner Should Work with a Fencing Contractor
Cleaning for Compliance, Not Just Comfort
It’s tempting to see cleaning as a soft service. Something nice to have. But legally, it’s tied to safety and compliance.
Under UK health and safety law, certain standards are non-negotiable. Clean, clear walkways. Proper air circulation. Safe handling of waste. If your site deals with chemicals or fine particles, the rules tighten.
This is where services help behind the scenes. They assist in staying aligned with COSHH requirements, prepare documentation for audits, and remove the sort of build-up that might trigger a formal notice.
And no, having a spotless breakroom won’t impress regulators if your extraction fans are clogged.
Working Around You, Not Against You
One thing people don’t think about until it’s too late—cleaning can get in the way. Machines switched off. Routes blocked. Noise.
Professional teams know how to avoid this. Some work in shifts. Others clean one section at a time. And yes, a few even clean overnight, when everything’s quiet.
The best setups are barely noticeable. They’ll:
- Isolate noisy equipment
- Dry floors fast, so no one slips
- Alert your team to hazard zones
- Finish the job without interrupting your output
When that happens, cleaning doesn’t feel like a chore—it becomes background support.
So, What’s Usually Covered?
The actual list of tasks depends on the place, but there are standard inclusions:
- Deep cleaning of industrial floors
- Surface and wall washing
- Degreasing near machinery
- Disinfection in shared zones
- Waste removal (including hazardous bins)
- Internal and external air duct cleaning
- Equipment wipe-downs (where approved)
You might also get a report after each clean. It’s useful when multiple departments share a space or when compliance records are needed.
They Handle the Jobs No One Else Will
There’s no polite way to say it—some of the tasks are grim. That’s the truth. But they still have to be done.
Drain blockages, pest-related mess, and heavy oil pooling under old compressors. All of that can fall under the cleaner’s responsibility.
That’s why proper training matters. It’s not just about getting the area spotless. It’s doing it safely. That includes:
- Avoiding cross-contamination
- Using biohazard disposal correctly
- Entering confined areas with permits
- Working at heights without cutting corners
The cleaner may not wear a suit and tie, but their certification list can be longer than most office staff.
How It Feels When It’s Done Right
This bit’s harder to define. You won’t always see the impact straight away. But after a full clean, the atmosphere shifts.
- The air smells less musty
- Workstations feel more organised
- You stop stepping around puddles or dust piles
- People notice, without quite knowing what changed
In some cases, teams get fewer complaints. Equipment runs more smoothly. Energy bills drop because vents aren’t blocked. It adds up in subtle ways.
Does It Cost Much?
Fair question. And no, there’s no single answer.
Prices swing based on:
- How often does the service happen
- How large or complex the site is
- Risk level (hazardous materials, roof access?)
- Whether cleaning happens during or after hours
But here’s something not everyone realises: skipping cleans doesn’t save money. It just postpones bigger repairs, downtime, or fines. Delays tend to come back harder.
One Last Point
This isn’t just about ticking a box. It’s about whether the place stays safe and functional. You wouldn’t let your machines run for months without servicing. The same logic applies here.
If the vents haven’t been touched in a year, or no one knows what’s under the conveyor belt—maybe it’s time to take a closer look.
After all, someone has to.