CNC Milling Service: Precision Machining for the Modern Manufacturing World
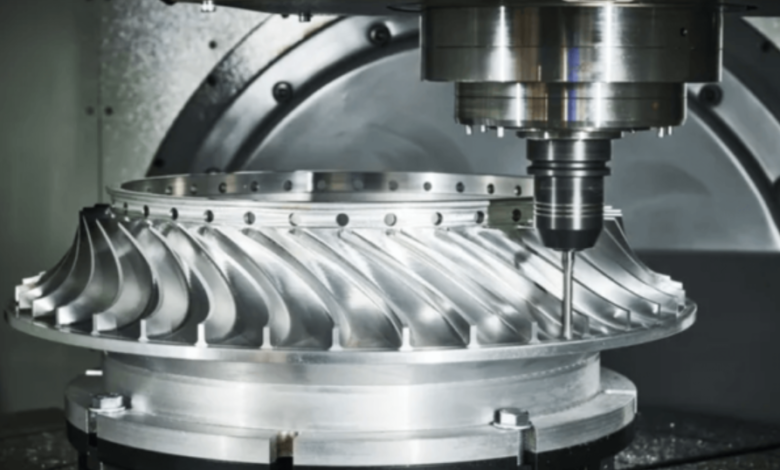
In today’s fast-paced industrial environment, the demand for highly accurate, complex components has never been greater. From the aerospace sector to the electronics and automotive industries, manufacturers require precision parts that meet tight tolerances and can be produced at scale. One of the most reliable solutions to meet this demand is the CNC milling service a process that combines the power of computer control with the versatility of milling operations to create intricate, high-performance parts.
This article explores how CNC milling service works, its key advantages, industrial applications, material compatibility, and why it’s a critical service in the age of Industry 4.0.
Understanding CNC Milling Service
CNC milling is a subtractive manufacturing process that uses rotating cutting tools to remove material from a solid workpiece. The machine is guided by a pre-programmed software (usually CAD/CAM files), which ensures the precise movement of tools along multiple axes (X, Y, Z—and in more complex setups, A and B axes). The result is a component with exact dimensions, surface finish, and intricate geometry.
A CNC milling service refers to a professional offering by machine shops or manufacturers who own and operate CNC milling machines for producing parts based on customer specifications. These services can be tailored for prototyping, low-volume manufacturing, or mass production.
See also: The Future of Door Access: How Technology is Securing Modern Spaces
Advantages of Using a CNC Milling Service
Choosing a reliable CNC milling service can offer several important benefits:
✅ Precision and Accuracy
CNC machines are capable of working with tolerances as tight as ±0.001 inches. This level of precision is especially critical in sectors like aerospace and medical devices.
✅ Repeatability
Once a program is created, the machine can produce hundreds or even thousands of identical parts with consistent quality.
✅ Flexibility
CNC milling service providers can accommodate a wide range of part sizes, materials, and complexities. Whether it’s a one-off prototype or a production run, the process adapts easily.
✅ Reduced Lead Time
Automation significantly cuts down production time. Once the digital file is uploaded, machining can begin almost instantly.
✅ Cost Efficiency at Scale
While setup costs can be higher for small batches, CNC milling becomes increasingly economical for medium to large volume production.
Key Industries That Rely on CNC Milling Services
A variety of industries benefit from outsourcing their machining needs to CNC milling service providers:
1. Aerospace and Defense
Complex parts such as brackets, housings, and turbine blades require high-precision machining. CNC milling is ideal for working with aerospace-grade materials like titanium and Inconel.
2. Automotive
From gear housings to engine mounts and dashboards, the automotive industry depends on CNC-milled parts for performance, reliability, and cost-effectiveness.
3. Medical and Healthcare
Surgical instruments, orthopedic implants, and diagnostic devices are often manufactured using CNC milling services due to their demand for precision and hygiene.
4. Consumer Electronics
Enclosures, connectors, and internal mechanical parts for smartphones and laptops require tight tolerances and perfect finishes—well within the capabilities of CNC milling.
5. Industrial Machinery
Components like flanges, shafts, and bearings that endure stress and wear are typically made through CNC milling for strength and exact fitment.
Types of CNC Milling Machines in Service
Depending on the complexity and volume of the parts, a CNC milling service provider may use several different types of machines:
➤ 3-Axis CNC Mills
These machines can move a cutting tool in the X, Y, and Z directions. They’re ideal for flat surfaces and relatively simple parts.
➤ 4-Axis CNC Mills
In addition to the basic three axes, these machines can rotate the workpiece around one axis (usually the A-axis). This allows for more complex geometries without repositioning the part.
➤ 5-Axis CNC Mills
These advanced machines can rotate on two additional axes (A and B), enabling the machining of highly complex and intricate components in a single setup.
Materials Compatible with CNC Milling Services
A CNC milling service provider typically offers machining for a broad range of materials, including:
- Metals: Aluminum, stainless steel, brass, copper, titanium, mild steel, and tool steel.
- Plastics: ABS, Nylon, POM (Delrin), PTFE (Teflon), PEEK, and polycarbonate.
- Composites and Exotic Materials: For specialized applications in aerospace or medical fields.
The material you choose will influence not only the machining strategy but also tool selection, spindle speed, feed rate, and cost.
Tolerance, Surface Finish, and Inspection
High-end CNC milling services provide more than just manufacturing—they also focus on quality control.
- Tolerances: Services can often hold dimensional tolerances of ±0.005 mm or tighter.
- Surface Finish: Ra values of 0.8 µm or better can be achieved, depending on the material and tooling.
- Inspection Reports: First article inspection (FAI), statistical process control (SPC), and coordinate measuring machine (CMM) reports are often included.
Design Considerations When Using a CNC Milling Service
To fully leverage the capabilities of a CNC milling service, it’s helpful to understand a few basic design guidelines:
- Avoid overly deep pockets or thin walls that are hard to mill.
- Design fillets with standard tool radii in mind.
- Use tolerances only where necessary—tight tolerances can raise costs.
- Include clearly defined datums in your CAD files for consistent referencing.
Most CNC milling service providers also offer Design for Manufacturability (DFM) feedback, which can help you optimize your part design for efficient machining.
The Digital Workflow of CNC Milling Services
Modern CNC milling services are fully digitized, and the workflow typically follows these steps:
- Design Upload: Clients upload CAD files (usually in STEP, IGES, or STL format).
- Quote Generation: Software or engineers analyze the file and generate a cost estimate.
- DFM Feedback: Optional step where the provider offers suggestions to improve design.
- Production: After approval, the machining begins.
- Quality Inspection: Each part is verified for dimensions, finish, and compliance.
- Packaging & Delivery: Final parts are shipped, usually within 5–10 business days.
Choosing the Right CNC Milling Service Provider
With so many options in the market, choosing the right CNC milling service can be daunting. Here are some key factors to evaluate:
- Experience: Look for providers with experience in your industry.
- Certifications: ISO 9001, AS9100, or medical certifications add credibility.
- Equipment Range: The wider the machine base, the more versatile the service.
- Customer Support: Transparent communication and DFM feedback are critical.
- Lead Time: Ensure their timeline matches your project schedule.
Final Thoughts
The demand for accurate, reliable, and cost-effective parts continues to rise, and CNC milling service providers are stepping in to meet that need with cutting-edge machinery, skilled technicians, and digital efficiency. Whether you’re building a prototype or producing tens of thousands of units, CNC milling is the cornerstone of modern manufacturing.
As innovation accelerates in industries like EVs, med-tech, and defense, CNC milling will continue to evolve, delivering faster turnaround, tighter tolerances, and higher-quality results than ever before.